When you’re designing a part that needs to be molded, the last thing you want is to get derailed late in the game because something was off—material, wall thickness, tolerances, or a design feature that’s impossible to mold. Plastic molding isn’t magic, but when it’s done right, it can feel pretty close.
This post breaks down what engineers and purchasers actually need to know: the different methods, common materials, where things usually go wrong, and what to expect from a trustworthy plastic injection molding service. If you’re an engineer or buyer sourcing molded parts, bookmark this one.
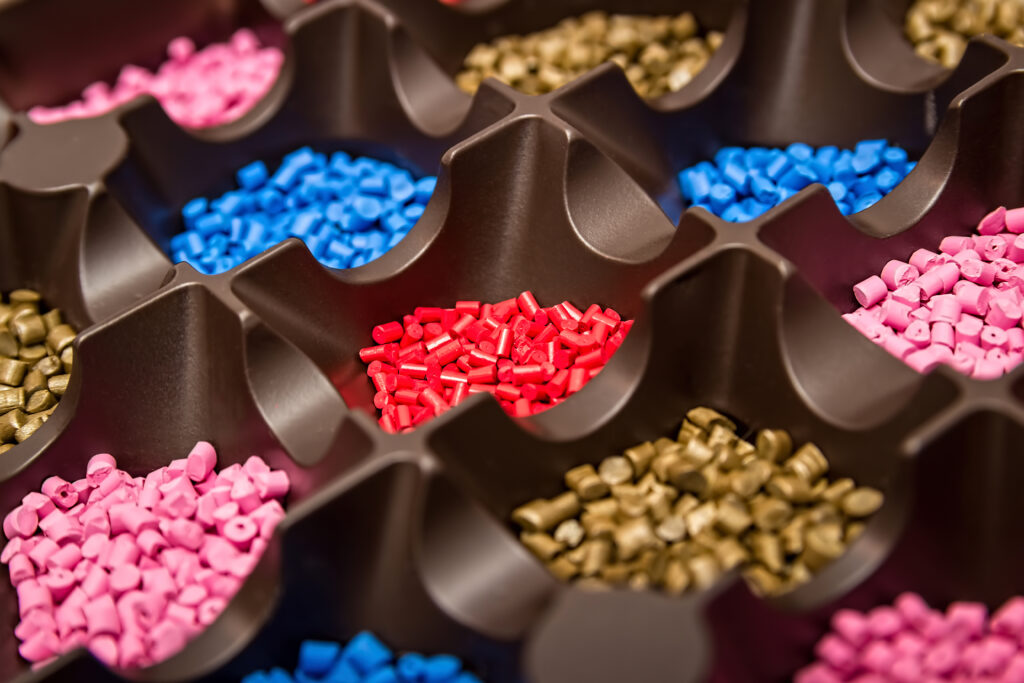
Understanding Plastic Molding Basics
Types of Plastic Molding Methods
There are several ways to turn raw plastic into functional parts, but the most common include:
- Plastic injection molding – Your go-to for high repeatability, tight tolerances, and high-volume production. Molten plastic is injected into a steel or aluminum mold under pressure and cooled into a final part.
- Overmolding/Insert molding – Ideal for combining materials (like soft grips over rigid structures or housing components with built-in features).
- Thermoforming – A flat plastic sheet is heated and shaped over a mold. Best for simpler geometries and larger parts at lower volumes.
Each method serves a specific need—choosing the right one early helps control cost and complexity.
When to Use Each Process
- Choose plastic injection molding when you need fine detail, repeatability, or complex geometries.
- Choose thermoforming for thinner-walled parts or when tooling budgets are limited.
- Use overmolding when performance, grip, or aesthetics require combining materials in one step.
Choosing the Right Thermoplastic
Common Thermoplastics in Plastic Molding
Choosing the wrong plastic leads to parts that crack, warp, or fail in the field. Here are the most commonly used materials in plastic molding:
- ABS – General-purpose workhorse with a good cost-to-performance balance.
- Nylon (PA) – High strength and wear resistance, often used in gears or structural parts.
- Polycarbonate (PC) – Excellent impact resistance and optical clarity.
- HDPE – Durable, chemical-resistant, great for containers or fluid applications.
- PEEK – High-end thermoplastic for medical, aerospace, and extreme environments.
Considerations When Selecting Materials
When choosing a thermoplastic for your project, you need to account for:
- Functional performance (load, temp, flexibility)
- Surface requirements (textured, clear, paintable)
- Compliance (FDA, UL, RoHS, etc.)
- Cycle time impact during plastic injection molding
A good plastic injection molding service will help match your design and performance requirements with the most cost-effective and reliable material.
Top 5 Design Mistakes in Plastic Molding
Even the best designs can fail in production. These are the five biggest missteps we see:
1. Inconsistent Wall Thickness
Unbalanced walls create warp and poor material flow. Maintain consistent wall thickness to reduce sink marks and short shots.
2. Ignoring Draft Angles
No draft = stuck part. At least 1–2° of draft is critical for mold release and preventing tool damage.
3. Overengineering Tolerances
Unnecessary tight tolerances drive up tooling costs and reject rates. Use them where functionally required—nowhere else.
4. Improper Rib and Boss Design
Too thick = sink marks. Too thin = weak. Follow known guidelines for boss diameter, spacing, and wall-to-rib ratios.
5. Poor Gate and Parting Line Planning
A badly placed gate or parting line can ruin appearance and function. Don’t wait until the mold is cut to fix this—collaborate early with your plastic injection molding service.
What to Expect from a Plastic Injection Molding Service
A full-service plastic injection molding service should offer more than just presses and parts:
- DFM reviews: They should proactively flag risks and offer design suggestions
- Material selection guidance: Based on part geometry and end-use conditions
- Tooling expertise: Including quick-turn prototype tools, bridge tooling, and high-volume production molds
- Responsive communication: You want collaboration—not radio silence
Why Engineers Should Collaborate Early with Their Molder
Looping in your molder once the design is “final” is like inviting the chef after the meal’s been served. Here’s why collaboration pays off:
- Shorter timelines: You get ahead of tool changes and prevent design revisions
- Fewer surprises: Engineers can balance ideal function with moldability
- More control: A trusted plastic injection molding service helps avoid delays, rework, and finger-pointing between design and manufacturing
At Mako, we collaborate from the CAD stage forward—not just when you’re ready to quote.
Final Thoughts + Resources
If you’re in charge of part performance, cost, or timeline, plastic molding decisions aren’t just technical—they’re strategic. Knowing the right method, material, and service partner makes a huge difference.
Whether you’re a product designer, engineer, or purchasing lead, working with a team that understands plastic injection molding inside and out is what takes you from part concept to successful production.
📎 Want a deeper look at our process, equipment, and engineering support? Contact us Today!
Download the Mako Plastics Capabilities Sheet and see how we help customers get from quote to part—faster and smarter.