Custom Plastic Parts Manufacturer: What to Look For
Custom solutions. Optimized designs. Seamless plastic injection molding from quote to delivery. ISO 9001:2015 Certified. Made in Canada. Made in the USA. Get a Quote in 48 Hours.
Rising labor costs, supply chain disruptions, and sustainability demands have made sourcing plastic components more complex than ever. Your manufacturing partner must become a strategic extension of your product team.
A custom plastic parts manufacturer does more than deliver parts. The right partner reduces risk, shortens production timelines, and identifies opportunities for cost savings—often through more innovative design and material selection.
Whether you’re producing components for consumer goods, construction, or medical devices, a manufacturer with the right expertise, equipment, and reliability can impact your results from day one.
Here’s what to look for when selecting a plastic manufacturing partner.
Experience and Capabilities Under One Roof
Start by examining the manufacturer’s scope of capabilities.
Do they simply mold parts, or do they also handle tooling, assembly, packaging, and shipping?
A fully integrated manufacturing process ensures your product receives consistent attention at every stage.
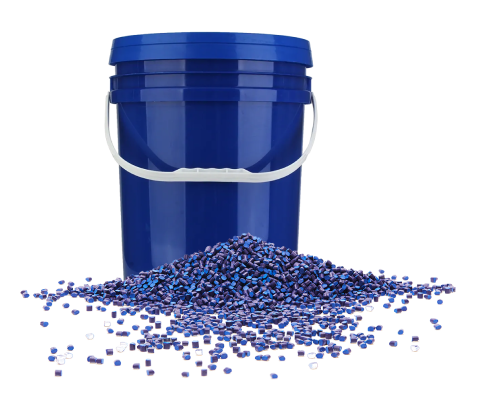
An ideal custom plastic parts manufacturer should offer:
- Custom plastic injection molding
- Overmolding and specialized applications
- Component assembly and custom packaging
- Silk screen printing, branding, and labeling
- Inventory management and fulfillment
Additionally, consider the company’s level of experience. Long-standing companies typically have deep insight into design-for-manufacturability, material selection, and process optimization. They’ll be able to guide your product development rather than simply follow orders.
Equipment, Certifications, and Sustainability
Your product’s performance depends on the right combination of technology and materials.
Start by confirming that the manufacturer uses a wide range of injection molding machines, from small to large tonnage (e.g., 100 to 1,250 tons). This flexibility supports different part sizes, applications, and volume production needs.
Also ask about their expertise with various plastic materials
:
- Chemical resistance
- Strength-to-weight ratio
- Thermal durability
- Compliance requirements
The injection molding process must align with both the chosen material and the product’s functional demands. For example, components used in medical waste disposal, cosmetics, or industrial systems all require tailored materials and specialized manufacturing approaches.
A qualified partner understands how to match each material to the right process, ensuring durability, performance, and regulatory compliance from the start.
Cost-Effective Solutions and Transparent Lead Times
A reliable custom plastic parts manufacturer will know how to maximize cost savings without cutting corners by:
- Offering design-for-manufacturability reviews
- Helping reduce material waste
- Managing labor costs through efficient workflows
Some manufacturers even cover tooling expenses in long-term partnerships—a major benefit for businesses managing tight budgets during product development.
Equally important are realistic lead times. Delays in plastic part delivery can halt downstream production, leading to lost revenue. Choose a partner that:
- Provides fast quotes (within 48 hours)
- Sets clear schedules for every production
- Tracks and reports delivery performance
Communication, Industry Fit, and Long-Term Alignment
A strong working relationship is just as important as technical ability. Pay attention to how well a manufacturer listens, asks questions, and collaborates in the early stages. If communication is slow now, it’s unlikely to improve during production.
Questions to ask yourself:
- Will the company assign a dedicated point of contact?
- Do they respond clearly and on time?
- Are they offering suggestions or just taking orders?
Experience in your specific industry can make a real difference. Manufacturers familiar with your market are more likely to meet compliance standards, anticipate design challenges, and understand application-specific demands.
Ultimately, the best custom plastic parts manufacturers build partnerships. They treat your project like it matters because they know your success is tied to theirs.
Need more information?
Download our brochure or contact us through our form to start the conversation.