If your parts fail in testing, you’ll face downstream delays and expensive rework. Prototype injection molding allows teams to evaluate part performance using the same materials, tolerances, and geometry intended for production.
This process provides the data and feedback required to make precise decisions before scaling becomes costly.
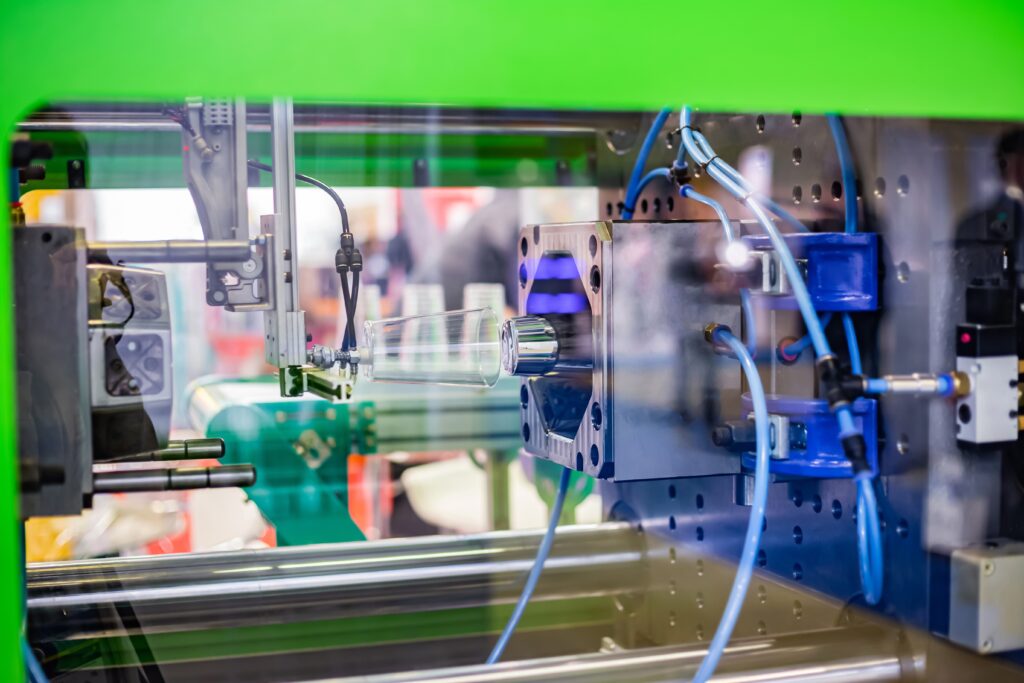
What Is Prototype Injection Molding?
Injection molding is the process of using temporary molding tools to produce low-volume, functional plastic parts. With a prototype mold, you can make parts that meet your injection molding design specs and then test them in real-world conditions, all without waiting months or investing in expensive production tooling.
This method uses a mold cavity to produce plastic parts through injection. It exposes weaknesses in material selection, highlights issues with wall thickness, and confirms manufacturability under realistic conditions.
If you don’t use injection molding to prototype, you’re not testing the real product; you’re testing an approximation. And if you don’t solve these issues during prototyping, you will face them again at full scale, with higher costs and longer lead times.
Why Prototype Injection Molding Matters for Product Development
- Speed: With simplified mold materials, you can move from concept to rapid prototype in a matter of weeks.
- Cost Savings: A prototype mold costs far less than a production injection molding tool.
- Design Validation: Evaluate part design, test for strength, fit, and function.
- Risk Reduction: Catch problems early and iterate quickly.
How Is Injection Molding Different from Full-Scale Production?
The main differences are in the tooling and the volume of parts.
Tooling Materials
Prototype molds are made from aluminum or soft steel, while production injection molding uses hardened steel built to last for hundreds of thousands of cycles.
Mold Cavity Life
Prototype molds have a short lifespan, ideal for smaller runs used in validation and pre-market testing.
Lead Time and Cost
Prototype molds can often be built and put into use within 2 to 4 weeks. This is faster than the several weeks or months typically required for the production of hardened steel molds. They’re also more affordable upfront, making them a lower-risk investment.
When Should I Choose Prototype Injection Molding Over 3D Printing or CNC Machining?
Each prototyping method serves a purpose, but they’re not alike. 3D printing is best suited for early-stage models when speed and low cost are more important than function. However, these parts often lack the necessary strength, material accuracy, or surface finish required for rigorous testing.
CNC machining delivers high precision and is ideal for prototypes made from solid materials. However, it becomes costly and less efficient when working with plastics, especially when the part has complex geometries.
Prototype injection molding stands out when your goal is to replicate the performance, materials, and finish of a final product and to test how it behaves under real production conditions. It’s the only method that closely mirrors the full-scale process, using real mold cavities, production-grade plastics, and your final part design.
Choosing the right prototyping method depends on what you’re solving for. If you’re still refining wall thickness, optimizing flow, or confirming fit and function, a prototype mold provides the most realistic and reliable results before committing to high-volume production.
What Materials Do Prototype Molds Use?
Material choice depends on design, function, and industry standards.
Common plastics used include:
- ABS
- Polycarbonate
- Polypropylene
- Nylon
Utilize sustainable materials, such as bio-based plastics, to minimize environmental impact without compromising performance.
Why Prototype Injection Molding Works
Companies like Mako Plastics use injection molding to help clients bridge the gap between concept and commercialization. From molding tool creation to assembly and shipping, the Mako Plastic team handles the entire process.
It’s faster than CNC, more accurate than 3D printing, and gives you a head start on high-volume manufacturing. Whether you’re launching a new device or optimizing an existing design, this method helps you get to market faster and smarter.
Considering injection molding? Schedule a consultation with Mako Plastics to explore your options.